When 3D printing is combined with machine learning, magic happens at the nano scale.
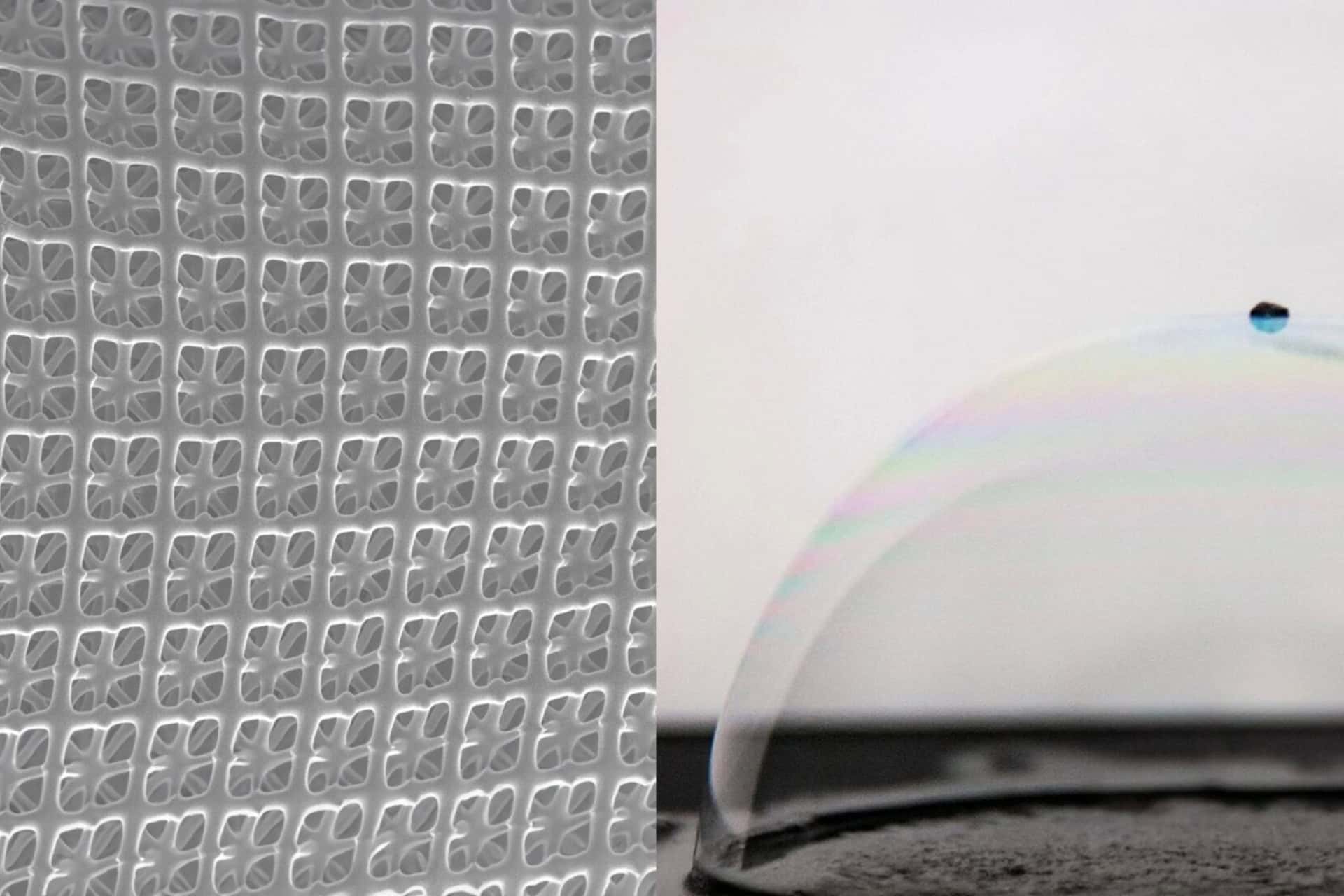
A team of Penn State researchers has used a new 3D-printing method to produce a complex metal build that was once only possible with welding: fusing two metals together into a single structure.
Using an advanced additive manufacturing process known as multi-material laser powder bed fusion—enabled by a newly acquired system in Penn State’s Center for Innovative Materials Processing Through Direct Digital Deposition (CIMP-3D)—the researchers printed a complex structure out of a blend of low-carbon stainless steel and bronze, which consists of 90% copper and 10% tin.
The researchers have published their approach in npj Advanced Manufacturing.
From seat cushions to mattresses to insulation, foam is everywhere—even if we don’t always see it. Now, researchers at The University of Texas at Dallas have fused chemistry with technology to create a 3D-printed foam that is more durable and more recyclable than the polymer foam found in many everyday products.
The research, published in RSC Applied Polymers, focused on creating a sturdy but lightweight foam that could be 3D-printed, a method that is still largely unexplored in commercial manufacturing, said the study’s co-lead author, UT Dallas doctoral student Rebecca Johnson BS’20.
“This is probably the longest project I’ve ever done,” said Johnson, who plans to complete her Ph.D. in chemistry in May. “From start to finish, it was a little over two years. A lot of it was trying to get the polymer formulation correct to be compatible with the 3D printer.”
A team of MIT researchers recently created the first synthetic muscle actuator that can flex in multiple directions. This study opens the door for more capable soft robots and other advanced medical breakthroughs. Here’s how the team utilized a new 3D printing method, alongside specially made stamps, to grow synthetic muscles in the lab that can replicate the real thing.
Understanding Muscle Architecture and Movement
To understand why you can’t just make a motor that does what a muscle does, you first need to look at how your body operates. When you move your hand, there is a lot more going on than just your muscles pulling in a single direction. Many multidirectional skeletal muscle fibers form intricate patterns and are mounted at angles to produce the exact motions of the human body.
Researchers at the UAB have developed a new chemical reaction to form solid polymeric networks using light (photocuring) which will allow the preparation of solid materials with controlled shapes measuring under a thousandth of a millimeter. The research is key for the development of new, performance-enhanced lithographic and 3D printing techniques.
At present, 3D printing is an increasingly widespread and accessible technology, typically involving the formation of solid polymeric materials in a specific region, either by extruding pre-formed polymers or by generating them in situ from their corresponding monomers, the molecules that make up polymers.
However, these techniques often suffer from several drawbacks, such as long printing times or low resolution, preventing the production of printed materials with micrometric dimensions.
A collaborative team of architects and builders has completed the first fully 3D-printed residential home in Auckland, New Zealand, and it’s also the largest building of that type in the Southern Hemisphere.
The Paremoremo home, named after the semi-rural suburb where it’s located, was highlighted by Home Magazine NZ in a short video. The low-slung, one-story residence spans over 2,700 square feet on a north-facing hill and incorporates smooth curved geometric surfaces that were facilitated by the novel 3D-printing process.
Tim Dorrington of Dorrington Atcheson Architects chose a concrete block form design due to the low cost and ease of construction, enlisting 3D-printed concrete specialist QOROX for their first full-sized home build.
It’s difficult to build devices that replicate the fluid, precise motion of humans, but that might change if we could pull a few (literal) strings. At least, that’s the idea behind “cable-driven” mechanisms in which running a string through an object generates streamlined movement across an object’s different parts. Take a robotic finger, for example: You could embed a cable through the palm to the fingertip of this object and then pull it to create a curling motion.
While cable-driven mechanisms can create real-time motion to make an object bend, twist, or fold, they can be complicated and time-consuming to assemble by hand. To automate the process, researchers from MIT’s Computer Science and Artificial Intelligence Laboratory (CSAIL) have developed an all-in-one 3D printing approach called “Xstrings.” Part design tool, part fabrication method, Xstrings can embed all the pieces together and produce a cable-driven device, saving time when assembling bionic robots, creating art installations, or working on dynamic fashion designs.
In a paper to be presented at the 2025 Conference on Human Factors in Computing Systems (CHI2025), the researchers used Xstrings to print a range of colorful and unique objects that included a red walking lizard robot, a purple wall sculpture that can open and close like a peacock’s tail, a white tentacle that curls around items, and a white claw that can ball up into a fist to grab objects.
Prototyping large structures with integrated electronics, like a chair that can monitor someone’s sitting posture, is typically a laborious and wasteful process.
One might need to fabricate multiple versions of the chair structure via 3D printing and laser cutting, generating a great deal of waste, before assembling the frame, grafting sensors and other fragile electronics onto it, and then wiring it up to create a working device.
If the prototype fails, the maker will likely have no choice but to discard it and go back to the drawing board.
New research from India has made it 10 times cheaper to construct buildings on-site using a 3D printer.
A report from The Better India highlights the work of Dr. Pradeepkumar Sundarraj, who built the Kelvin6K Pro. It’s India’s first on-site construction 3D printer that can build a 2,500-square-foot home in less than 30 days.