Standard silkworm silk has been made stronger than spider’s silk, one of the toughest materials known, by bathing it with metals and respinning it.
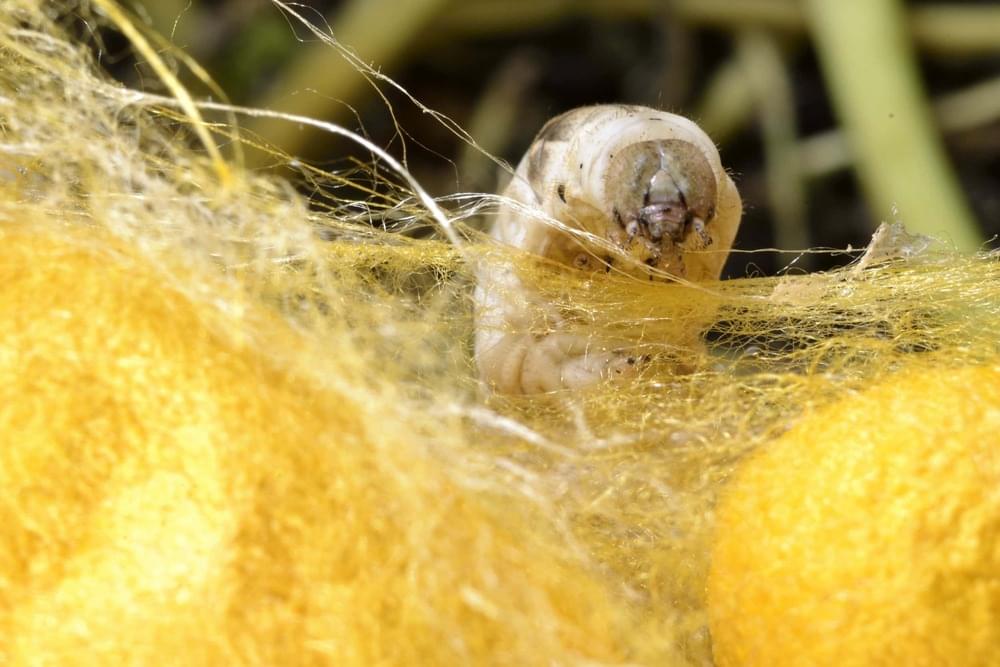
Some solid materials have a memory of how they have previously been stretched out, which impacts how they respond to these kinds of deformations in the future. A new Penn State study lends insight into memory formation in the foams and emulsions common in food products and pharmaceuticals and provides a new method to erase this memory, which could guide how materials are prepared for future use.
“A crease in a piece of paper serves as a memory of being folded or crumpled,” said Nathan Keim, associate research professor of physics at Penn State who led the study. “A lot of other materials form memories when they are deformed, heated up, or cooled down, and you might not know it unless you ask the right questions. Improving our understanding of how to write, read, and erase memories provides new opportunities for diagnostics and programming of materials. We can find out the history of a material by doing some tests or erase a material’s memory and program a new one to prepare it for consumer or industrial use.”
The researchers studied memory in a type of material called disordered solids, which have particles that are often erratically arranged. For example, ice cream is a disordered solid made up of a combination of ice crystals, fat droplets, and air pockets mixed together in a random way. This is in stark contrast to materials with “crystalline structures,” with particles arranged in highly ordered rows and columns. Disordered solids are common in food sciences, consumer products, and pharmaceuticals and include foams like ice cream and emulsions like mayonnaise.
Add analog and air-driven to the list of control system options for soft robots.
In a study published online this week, robotics researchers, engineers and materials scientists from Rice University and Harvard University showed it is possible to make programmable, nonelectronic circuits that control the actions of soft robots by processing information encoded in bursts of compressed air.
“Part of the beauty of this system is that we’re really able to reduce computation down to its base components,” said Rice undergraduate Colter Decker, lead author of the study in the Proceedings of the National Academy of Sciences. He said electronic control systems have been honed and refined for decades, and recreating computer circuitry “with analogs to pressure and flow rate instead of voltage and current” made it easier to incorporate pneumatic computation.
Clouds are made of silicate minerals.
The clouds of the distant brown dwarf contain silicate material, making it a quite unusual atmospheric composition.
Scientists have discovered a fluorescent protein that flouts trade-off relationships.
Scientific research institute RIKEN produced bright and photostable green fluorescent protein from Japanese jellyfish. Published in Nature Biotechnology.
Proteins that emit green light when illuminated are effective instruments for capturing images of intricate cell architecture. Such fluorescent proteins can be attached to target structures of interest, which light up when exposed to blue light.
Kuroshio Biological Research Foundation.
Published in Nature Biotechnology on August 17, the results show that the protein maintaining its brightness even when irradiated by high light has significant implications for fluorescence imaging of biological material.
Breakthrough opens up new possibilities for the creation of next-generation materials.
A new way to self-assemble particles has been created by a team of physicists. This advance offers new promise for building complex and innovative materials at the microscopic level.
Self-assembly, introduced in the early 2000s, gives scientists a means to “pre-program” particles, which allows for the construction of materials without further human intervention. This is basically the microscopic equivalent of Ikea furniture that can assemble itself.
A method to draw data in an area smaller than 10 nanometers has been proposed in a recent study published in Physical Review Letters
A joint research team led by Professor Daesu Lee (Department of Physics) of POSTECH, Professor Se Young Park (Department of Physics) at Soongsil University, and Dr. Ji Hye Lee (Department of Physics and Astronomy) of Seoul National University has proposed a method for densely storing data by “poking” with a sharp probe. This method utilizes a material in the metastable state, whose properties change easily even with slight stimulation.
A thin film of metastable ferroelectric calcium titanate (CaTiO3) enables the polarization switching of a material even with a slight pressure of a probe: A very weak force of 100 nanonewtons (nN) is more than enough. The joint research team succeeded in making the width of the polarization path smaller than 10 nm by using this force and found the way to dramatically increase the capacity of data storage. This is because the smaller the size of the path, the more data the single material can store.
A physicist’s do-it-yourself art project makes vibrant images with a pair of polarizers and carefully placed layers of transparent tape.
When the COVID-19 pandemic shut down universities and offices across the world in spring 2020, finding new hobbies to stave off fear (and boredom) became paramount. While some took up cross-stitch or a new stretching routine, Aaron Slepkov, a photonics researcher at the University of Trent in Peterborough, Canada, turned to a physics-inspired art form called polage to occupy his time.
Polage, or polarization-filtered coloration, as Slepkov calls it, is a kind of collage that uses polarizers and thin films to create brightly colored artworks that transform depending on how you look at them. This metamorphosis is made possible by birefringence, an optical property of certain materials that changes the polarization state of transmitted light. Examples of birefringent materials include ice, calcite crystals, cellophane film, and transparent tape.
For billions of years, the Milky Way’s largest satellite galaxies—the Large and Small Magellanic Clouds—have followed a perilous journey. Orbiting one another as they are pulled in toward our home galaxy, they have begun to unravel, leaving behind trails of gaseous debris. And yet—to the puzzlement of astronomers—these dwarf galaxies remain intact, with ongoing vigorous star formation.
“A lot of people were struggling to explain how these streams of material could be there,” said Dhanesh Krishnarao, assistant professor at Colorado College. “If this gas was removed from these galaxies, how are they still forming stars?”
With the help of data from NASA’s Hubble Space Telescope and a retired satellite called the Far Ultraviolet Spectroscopic Explorer (FUSE), a team of astronomers led by Krishnarao has finally found the answer: the Magellanic system is surrounded by a corona, a protective shield of hot supercharged gas. This cocoons the two galaxies, preventing their gas supplies from being siphoned off by the Milky Way, and therefore allowing them to continue forming new stars.